Head of Manufacturing Excellence (Plant cluster in IAA region)
Siemens
Date: 3 weeks ago
City: Thāne, Maharashtra
Contract type: Full time
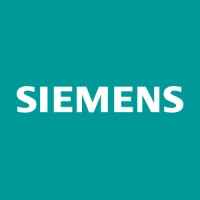
Job Title: Head of Manufacturing Excellence (Plant cluster in IAA region)
Location: Base Mumbai
Travel: Up to 50% (expected to travel frequently between plants within the assigned cluster)
Reports To:, IAA Segment Manufacturing plant cluster Head
Job Summary:
The Head of Manufacturing Excellence (Cluster) is a critical leadership role responsible for driving operational excellence, continuous improvement, and a culture of high performance across a designated cluster of manufacturing plants. This individual will lead the development and execution of manufacturing excellence strategies, methodologies, and initiatives to optimize processes, improve quality, reduce costs, enhance safety, and foster a sustainable continuous improvement mindset throughout the cluster. The successful candidate will act as a change agent, mentor, and expert, collaborating closely with plant leadership teams to achieve world-class manufacturing standards.
Key Responsibilities:
Education: Bachelor's degree in Engineering (Industrial, Mechanical, Electrical, Chemical, or Manufacturing preferred) or a related technical field. Master's degree (e.g., MBA, Operations Management) is a plus. Experience: Certifications: Skills:
Location: Base Mumbai
Travel: Up to 50% (expected to travel frequently between plants within the assigned cluster)
Reports To:, IAA Segment Manufacturing plant cluster Head
Job Summary:
The Head of Manufacturing Excellence (Cluster) is a critical leadership role responsible for driving operational excellence, continuous improvement, and a culture of high performance across a designated cluster of manufacturing plants. This individual will lead the development and execution of manufacturing excellence strategies, methodologies, and initiatives to optimize processes, improve quality, reduce costs, enhance safety, and foster a sustainable continuous improvement mindset throughout the cluster. The successful candidate will act as a change agent, mentor, and expert, collaborating closely with plant leadership teams to achieve world-class manufacturing standards.
Key Responsibilities:
- Strategy Development & Deployment:
- Develop and implement a comprehensive manufacturing excellence strategy for the assigned cluster, aligned with overall company goals and global manufacturing excellence frameworks.
- Identify key opportunities for improvement across all plants within the cluster, focusing on safety, quality, delivery, and cost (SQDC).
- Translate strategic objectives into actionable plans and initiatives for each plant.
- Operational Excellence Leadership:
- Lead the implementation and sustainment of Lean, Six Sigma, TPM (Total Productive Maintenance), Industry 4.0 concepts, and other continuous improvement methodologies across the cluster.
- Drive standardization of best practices, processes, and systems across all plants to ensure consistency and efficiency.
- Establish and monitor key performance indicators (KPIs) for manufacturing excellence, ensuring data-driven decision-making and accountability.
- Oversee and actively participate in root cause analysis for significant operational deviations, ensuring effective corrective and preventive actions.
- Team Development & Capability Building:
- Mentor, coach, and develop plant-level manufacturing excellence leaders, continuous improvement specialists, and operations teams.
- Build and strengthen the continuous improvement capabilities of plant personnel through training, workshops, and hands-on guidance.
- Foster a culture of continuous learning, problem-solving, and employee engagement in improvement initiatives.
- Project Management & Execution:
- Lead and facilitate high-impact improvement manufacturing related projects across the cluster, ensuring timely execution, achievement of targets, and sustainable results.
- Prioritize projects based on strategic impact and resource availability.
- Track project progress, report on savings, and ensure successful deployment of solutions.
- Collaboration & Stakeholder Management:
- Work closely with plant managers, MF operations, Process planning, Quality, Supply chain, EHS and other functional leaders to identify opportunities and drive cross-functional improvements.
- Act as a liaison between global manufacturing excellence initiatives and the cluster's specific needs.
- Present findings, recommendations, and progress reports to senior leadership.
- Benchmarking & Innovation:
- Stay abreast of industry best practices, emerging technologies, and new manufacturing excellence methodologies.
- Benchmark performance against industry leaders and identify opportunities for innovative solutions within the cluster.
- Promote knowledge sharing and collaboration across the cluster and with other clusters within the organization.
- Safety & Compliance:
- Champion a safety-first culture and ensure that all manufacturing excellence initiatives contribute to a safer working environment.
- Ensure compliance with all relevant industry regulations and company standards.
- Minimum of 12-15 years of progressive experience in manufacturing operations, with at least 5-7 years in a dedicated manufacturing excellence, continuous improvement, or Lean leadership role. Manufacturing in low voltage switchgear is highly essential.
- Proven experience overseeing multiple manufacturing sites or a cluster of plants.
- Demonstrated success in implementing and sustaining Lean, Six Sigma, TPM, or other operational excellence methodologies with quantifiable results.
- Experience in diverse manufacturing environments (e.g., high volume, low volume, discrete, process) is an advantage.
- Lean Expert or Master Black Belt certification is highly desirable.
- PMP certification is a plus.
- Deep understanding of Lean principles (Value Stream Mapping, 5S, Kaizen, SMED, Poka-Yoke, etc.), Six Sigma methodologies, and TPM.
- Knowledge of manufacturing technology for parts, assembly and function testing for low voltage electromechanical switchgear products.
- Strong analytical and problem-solving skills, with proficiency in statistical analysis tools (e.g., Minitab).
- Excellent leadership, communication (written and verbal), and interpersonal skills.
- Ability to influence without direct authority and drive change at all levels of the organization.
- Strong project management and organizational skills.
- Proficiency in Microsoft Office Suite (Excel, PowerPoint, Word, Visio).
- Familiarity with Industry 4.0 concepts, automation, and digital manufacturing tools.
- Ability to travel frequently within the assigned cluster of plants.
- Strategic thinker with a hands-on approach.
- Results-oriented and data-driven.
- Highly collaborative and a team player.
- Strong sense of ownership and accountability.
- Resilient, adaptable, and comfortable with ambiguity.
- Passionate about continuous improvement and developing people.
How to apply
To apply for this job you need to authorize on our website. If you don't have an account yet, please register.
Post a resumeSimilar jobs
Service Engineer - SAARC MEA
Blue Star MEA,
Thāne, Maharashtra
2 days ago
Job Description Candidate must be open to travel to different countries Technical Knowledge on Ducted, VRF & Chillers (Scroll, Screw, Centrifugal), Cold Room, inverter splits Knowledge of Refrigeration & Air conditioning functioning Knowledge of operating parameters products mentioned above Knowledge of electronics components identification & functions. Knowledge of complaint management Revenue generation through Spares & repair jobsKey Responsibilities Good Communication...
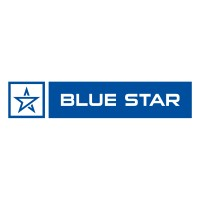
Technical Support Engineer
Sysnet Global Technologies Pvt Ltd,
Thāne, Maharashtra
1 week ago
Select TemplateWe are looking for a technical support engineer who can provide enterprise-level support to customers. You should have the ability to research, diagnose, troubleshoot, and resolve the issues to the clients’ satisfaction.Your Responsibilities Install, configure, monitor & maintain computer applications & networks Configure operating systems. Prioritize and manage the workflow along with resolving issues related to the network Diagnose,...
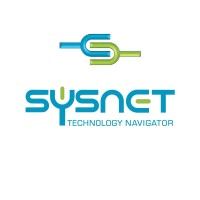
Technical Sales Support-Order Management
Siemens,
Thāne, Maharashtra
2 weeks ago
At Siemens Energy, we can. Our technology is key, but our people make the difference. Brilliant minds innovate. They connect, create, and keep us on track towards changing the world’s energy systems. Their spirit fuels our mission.Our culture is defined by caring, agile, respectful, and accountable individuals. We value excellence of any kind. Sounds like you?Technical Sales Support Professional-Kalwa-TR, Siemens...
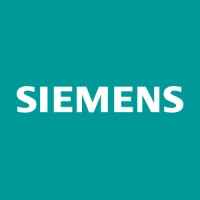