Manager – Manufacturing
PepsiCo
Date: 2 weeks ago
City: Patiāla, Punjab
Contract type: Full time
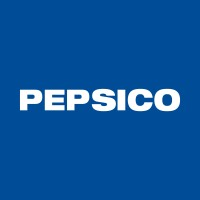
Overview
Job Overview:
Responsibilities:
People Management: Preparing multiskilling & detailed deployment plan of operatives through shift scheduling to drive operational discipline, cost & people capability. Driving the targets of Direct Labour cost & TPP, developing backups on redeployment matrix to impact on manpower productivity. Regular coordination with HR team on tracking unauthorized absenteeism and OT trend and ensuring effective communication to sustain good discipline. Participate actively during LTS and act as a frontline leader for the process.
Safety: Ensure 100% safety compliance in shopfloor and drive a positive Atmosphere towards Human Safety.
Production Deliverables: Ensuring compliance to weekly/ monthly production targets as per PepsiCo quality and hygiene standards, delivering SA over & above plan. Maximizing TE/ NE , ensuring conversion efficiencies better than AOP and executing ideas on productivity - sharing views with sector SMEs for troubleshooting and capturing better productivity ideas implemented across other plants as a part of continuous improvement. Coordinating & planning with cross functional team members to ensure seamless production.
Capacity Utilization: Maximizing NE TE by effectively scheduling production with LD & T Manager to optimize change over, monitoring & reducing NE TE losses & utilizing manpower planning in line with actual plan a capacity. Ensure and Update line platform matrix as per line capacity.
Waste Management: Ensuring minimal wastage, optimum manpower utilization and operating at maximum efficiencies. Driving for “ZERO Loss” mantra for the lines with the help of sector team and by utilizing TPM tools & ensuring cross functional involvement (focusing on JH culture on shop floor).
Line Availavility : Ensuring minimal Unplanned breakdown and close coordination with Maintenance manager to to drive a sustainable agenda to reduce the USDT in shopfloor. Ensuring the “Why Why Analysis” of b/d on timely manner & implement actions; practice JH to reduce breakdown. Ensure control on consumable cost.
Planning and Reporting: Ensuring integrity of data entry across lines, monitoring the data on shift to shift basis and reporting of the all the numbers on daily basis in DW as per MNW guidance.
IR management: Ensuring line discipline during production - OT, Absenteeism control, motivating the teams for the positive environment at the shop floor. Conducting 1-1 with the operatives, implementation of “Each one teach one”, on the shop floor for the better engagement and building inclusive culture & keeping the operation disruption free.
hygiene, safety & TPM culture that promotes company growth.
Cross functional coordination with Agro, LD & T, quality, Engineering, HR & Finance to smoothly run day to day production.
SAP management: Batch closing and stock verification in Day store, taking care of GCS, Corporate audit and KC compliances. Ensuring inventory management by proper transferring of FG and taking RM by proper hand shaking between the cross functional departments.
NPD handling: Ensuring compliance to all NPD production, reference and Gold sample production on timely manner with AOP efficiency numbers. Ensuring proper feedback to R&D to build upon the current standards.
Cost Management: controlling the consumables, parts change management and developing new vendors for the reduction in consumables, better quality of parts at the engineering stores with close coordination with engineering team and engineering store person and also sensitizing the shop floor team.
New projects: Acting as manufacturing representative for upcoming new projects.
Qualifications
Qualifications:
Job Overview:
- To ensure that all processes related to manufacturing are carried out smoothly at the Plant to consistently provide finished product that meets the business need (product availability, cost & quality) with applicable statutory requirements.
- To drive operational excellence processes in manufacturing (M&W/TPM/QMS/EMS) for continual improvement to move operations standards towards world class performance.
- Assisting HOD manufacturing in delivering productivity & driving a high performance culture at shop floor.
Responsibilities:
People Management: Preparing multiskilling & detailed deployment plan of operatives through shift scheduling to drive operational discipline, cost & people capability. Driving the targets of Direct Labour cost & TPP, developing backups on redeployment matrix to impact on manpower productivity. Regular coordination with HR team on tracking unauthorized absenteeism and OT trend and ensuring effective communication to sustain good discipline. Participate actively during LTS and act as a frontline leader for the process.
Safety: Ensure 100% safety compliance in shopfloor and drive a positive Atmosphere towards Human Safety.
Production Deliverables: Ensuring compliance to weekly/ monthly production targets as per PepsiCo quality and hygiene standards, delivering SA over & above plan. Maximizing TE/ NE , ensuring conversion efficiencies better than AOP and executing ideas on productivity - sharing views with sector SMEs for troubleshooting and capturing better productivity ideas implemented across other plants as a part of continuous improvement. Coordinating & planning with cross functional team members to ensure seamless production.
Capacity Utilization: Maximizing NE TE by effectively scheduling production with LD & T Manager to optimize change over, monitoring & reducing NE TE losses & utilizing manpower planning in line with actual plan a capacity. Ensure and Update line platform matrix as per line capacity.
Waste Management: Ensuring minimal wastage, optimum manpower utilization and operating at maximum efficiencies. Driving for “ZERO Loss” mantra for the lines with the help of sector team and by utilizing TPM tools & ensuring cross functional involvement (focusing on JH culture on shop floor).
Line Availavility : Ensuring minimal Unplanned breakdown and close coordination with Maintenance manager to to drive a sustainable agenda to reduce the USDT in shopfloor. Ensuring the “Why Why Analysis” of b/d on timely manner & implement actions; practice JH to reduce breakdown. Ensure control on consumable cost.
Planning and Reporting: Ensuring integrity of data entry across lines, monitoring the data on shift to shift basis and reporting of the all the numbers on daily basis in DW as per MNW guidance.
IR management: Ensuring line discipline during production - OT, Absenteeism control, motivating the teams for the positive environment at the shop floor. Conducting 1-1 with the operatives, implementation of “Each one teach one”, on the shop floor for the better engagement and building inclusive culture & keeping the operation disruption free.
- Key Control: Ensuring KCs of manufacturing are maintained in letter & spirit.
- Ensuring compliance to food safety as per AIB guidance.
- Acting as a reliever: Relieving Shift In-charges as and when required.
- MNW & Other audit: Acting as a manufacturing control owner/ representative of MNW data; quality & safety audit.
hygiene, safety & TPM culture that promotes company growth.
Cross functional coordination with Agro, LD & T, quality, Engineering, HR & Finance to smoothly run day to day production.
SAP management: Batch closing and stock verification in Day store, taking care of GCS, Corporate audit and KC compliances. Ensuring inventory management by proper transferring of FG and taking RM by proper hand shaking between the cross functional departments.
NPD handling: Ensuring compliance to all NPD production, reference and Gold sample production on timely manner with AOP efficiency numbers. Ensuring proper feedback to R&D to build upon the current standards.
Cost Management: controlling the consumables, parts change management and developing new vendors for the reduction in consumables, better quality of parts at the engineering stores with close coordination with engineering team and engineering store person and also sensitizing the shop floor team.
New projects: Acting as manufacturing representative for upcoming new projects.
Qualifications
Qualifications:
- Education: BE / B Tech / with 6-8 years of experience in large scale operation in FMCG.
- Functional Experience: Approx. 6-8 years of experience
- Language: English, Hindi, Local language preferred
- Team player & ability to handle large pool of operatives.
- Excellent communication, both written and verbal.
- Negotiation skills & influencing ability.
- Interpersonal & coordination skill.
- Strong analytical skills.
How to apply
To apply for this job you need to authorize on our website. If you don't have an account yet, please register.
Post a resumeSimilar jobs
Senior Relationship Executive - GL North West
Bajaj Finserv,
Patiāla, Punjab
2 days ago
Location Name: Devigarh - Main RoadJob Purpose“This position is open with Bajaj Finance ltd.”Duties And ResponsibilitiesХ To achieve given Sales nos through customer walk inХ Work closely with the branch Service executives to drive Gold loan customers for fulfillmentХ Ensuring policy adherence and meeting compliance requirementХ Tracking Approval rate & other critical SLA deliverables for Gold loan product.Х Supporting Assayer...
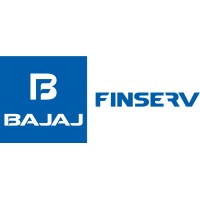
field sales officer(fmcg)
Bharrgava Global,
Patiāla, Punjab
₹20,000
-
₹30,000
per month
1 week ago
Skills:beauty, fmcg, personal care, Cosmetics, hair care, food beverage,profile- field sales officer (fmcg)salary-20k to 25klocation-patiala ,punjabexperience-2 year.................................................................................................................................................................................................................................................................................................................................................................................................................................................................................................................................................................................
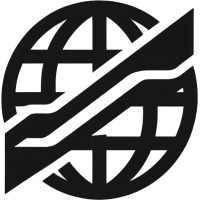
SC QC Sr Manager
PepsiCo India,
Patiāla, Punjab
3 weeks ago
JOB_DESCRIPTION.SHARE.HTMLCAROUSEL_PARAGRAPHJOB_DESCRIPTION.SHARE.HTMLPatiala, IndiaSupply Chain350868Yes - StandardNoJob DescriptionApply nowJoin Our Talent CommunityJOB_DESCRIPTION.SHARE.HTMLCAROUSEL_PARAGRAPHJOB_DESCRIPTION.SHARE.HTMLOverviewThis role will provide technical and Quality & Food Safety leadership for Channo COSO manufacturing site and help delivering AMESA sector QC vision “Drive Quality and Food safety Excellence to delight our consumers and customers.”Responsible to ensure food safety plans and policies at Channo unit are in alignment with PepsiCo policies...
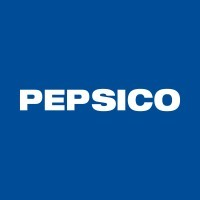